To stand still is to take a step back
The company suggestion scheme (BVW)
With his statement „Nothing on earth is stronger than an idea whose time has come“, Victor Hugo — a French author, alive from 1802 to 1885 — described exactly what we on the BVW team believe — or rather, what we want to experience with you.
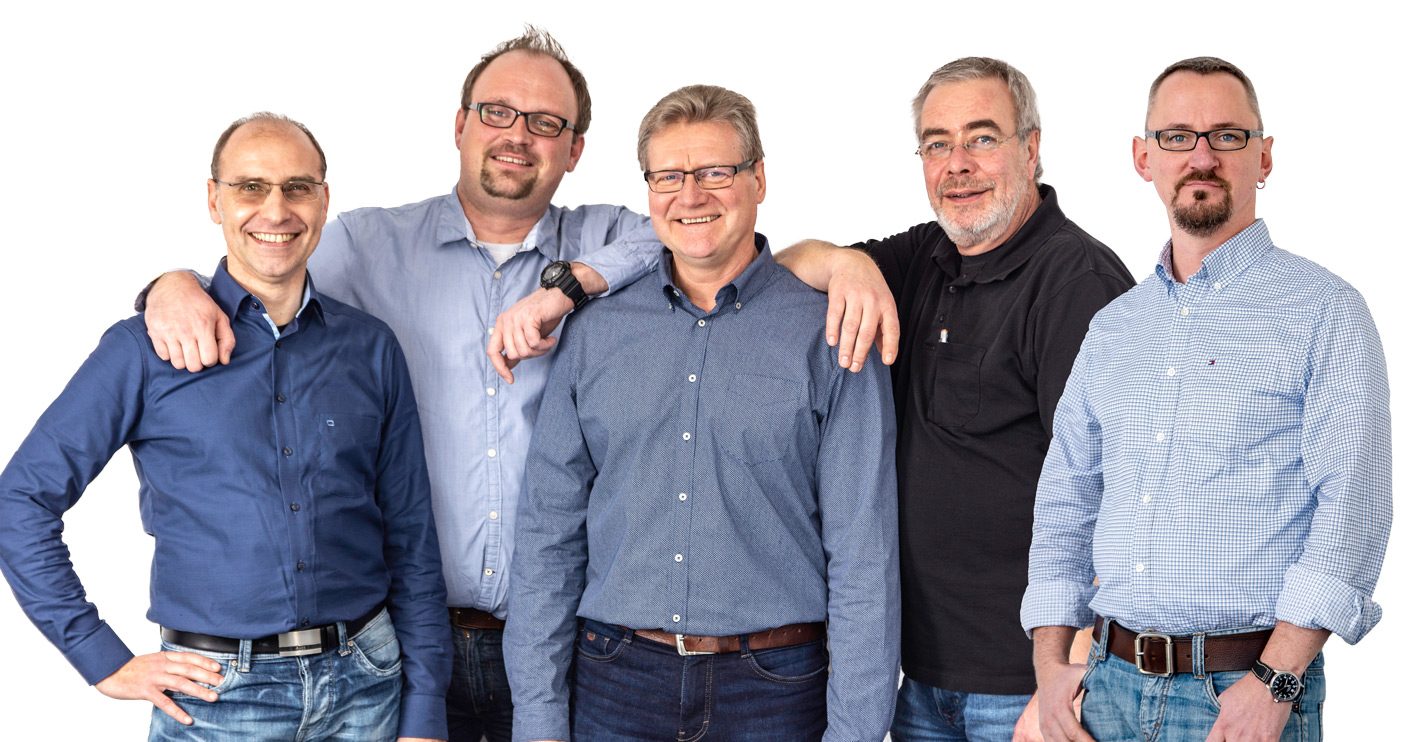
Ideas generally arise in places where problems or complicated processes make work harder or more complicated for those affected on a daily basis. Only specialists on site, at the plant or in the process can know what is complicated and annoying and how to improve it. We are in favour of the idea that an idea doesn‘t have to stay just an idea, simply because certain things „have always been done that way“.
Quite the opposite!
Every suggestion for improvement brought to us is checked and evaluated fairly. If there is a way to improve work routines or processes, or even the product itself, we will take all necessary steps to ensure that this idea does not remain just an idea.
In return for your trust in letting us be part of your ideas and allowing us to implement them for the organisation, we also believe that each idea that is implemented should be rewarded with an appropriate prize. As Rudolf von Bennigsen-Foerder , a German industrial manager, 1926–1989, once said: „To stand still is to take a step back“. We want to look towards a successful future together with you and
We can only prevent problems if we know about them.
2017 - 2019
Suggestions for improvement over the last three years
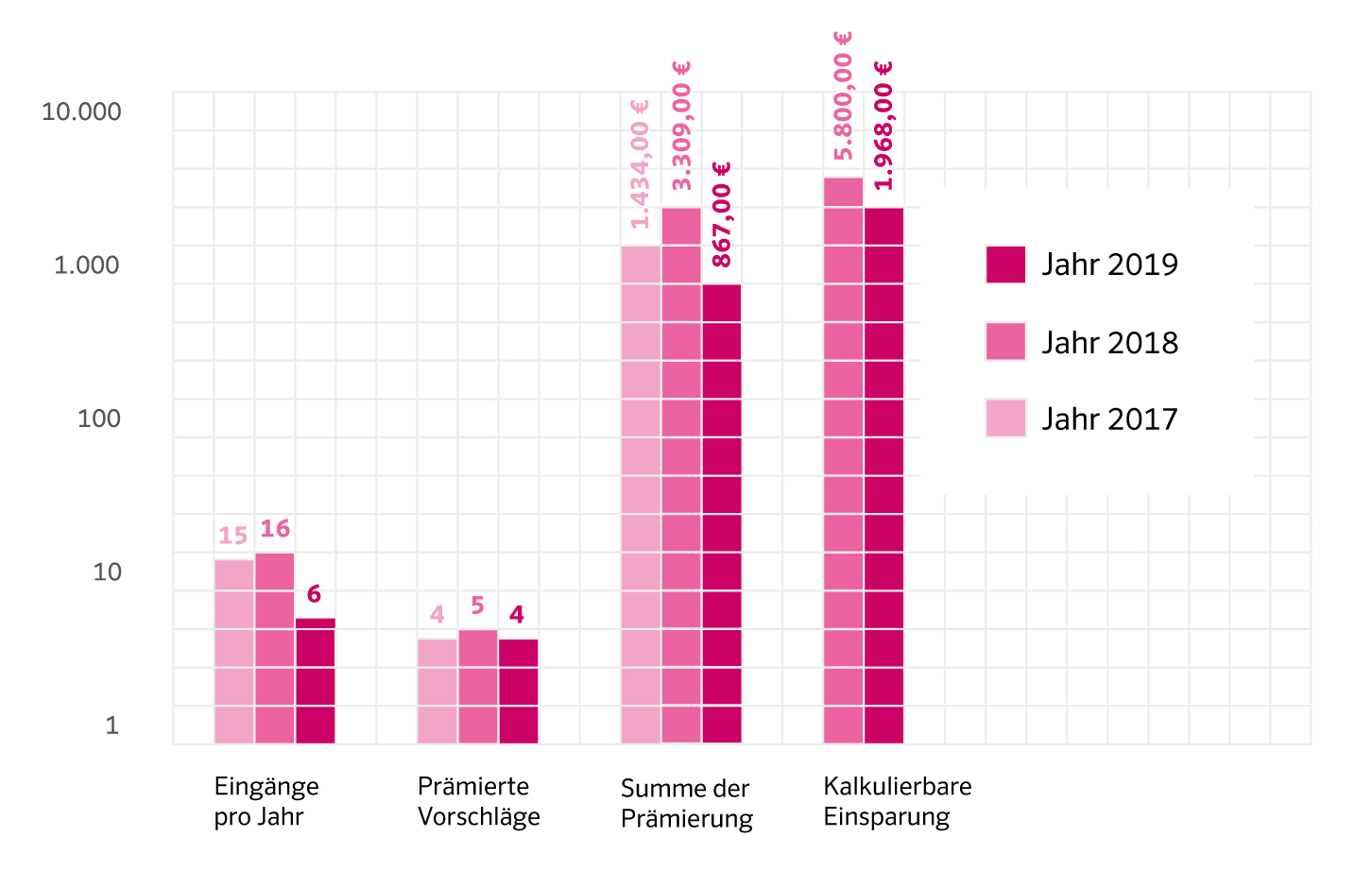
Description of photo
Most suggestions for improvement are connected to savings for the company. Often, these cannot be calculated, because we have to work with estimates. With the calculable savings above, this is not the case.
Suggestion for improvement
Suggestion for improvement Packaging optimisation
Submitted by
Eduard Stecker
Idea
Safe packaging alternative for the Twin-Boost valve body 108-035-0239
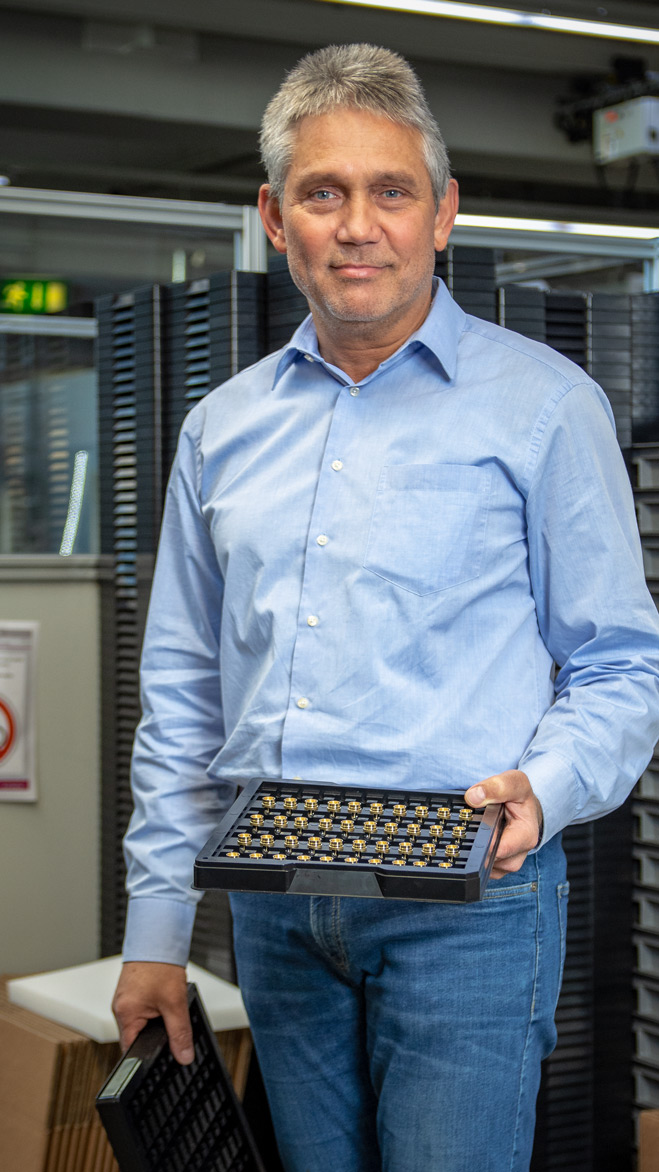
Optimisation
The idea of no longer packaging the Twin-Boost valve body in the C13 blister products, but instead using the existing anchoring system pallets, has clear advantages. Since the valve body had too much room to move in the old blister packaging and could, therefore, get mixed up, the solution using stable anchoring system pallets is a significant improvement.
The new anchoring system pallets prevent this effectively and are also more convenient in terms of internal transport and the storage location in manufacturing. This is an example of an optimisation that was achieved with existing equipment, which was rewarded with a prize.
Disadvantages of the previous C13 packaging 900-881-0092
- Size is awkward to handle
- Pallet is not strong enough for the heavy valve body
- Only 5000 pallets are available in the warehouse to fulfil the entire C13 demandLaut
According to statements by the person in charge of logistics, Dierk Dreyer, the pallets also cannot be washed and are, therefore, always purchased new. Moreover, a covering box is also required for every 180 units, with a base and lid. This leads to yet more additional costs.
Suggestion for improvement
Separate nitrogen plant
Submitted by
Marcel Wenda
Idea
To eliminate nitrogen bundles and operate a separate nitrogen plant
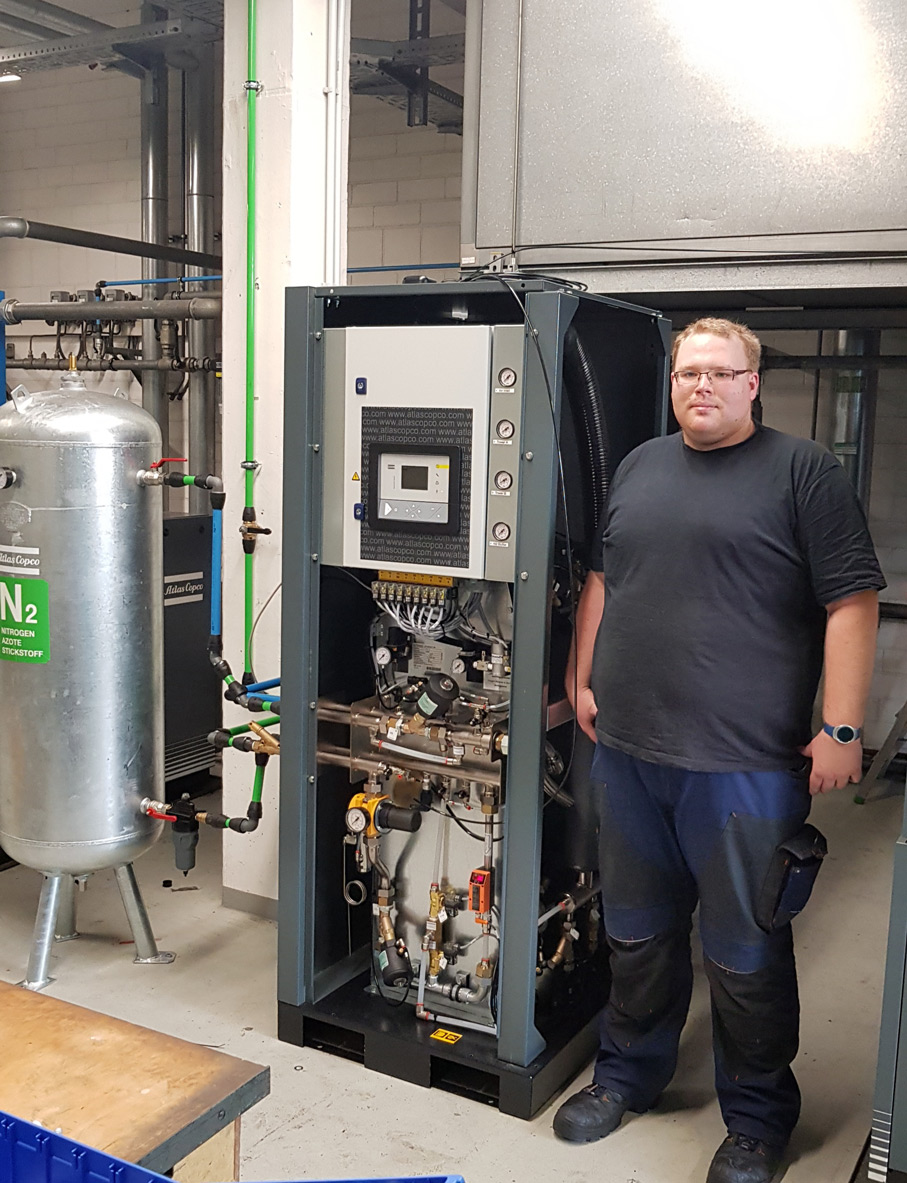
Optimisation
The investment of over €18,000 would yield a profit within less than two years, meaning that from as early as the third year, we could be registering savings of over €9000 per year.
With his suggestion for improvement, Mr Wenda advocated to automate the soldering process in our C30 plant yet further. The soldering process integrated in the plant requires a constant supply of nitrogen to ensure the required soldering quality. Originally, the nitrogen was provided through „nitrogen bundles“ that had to be replaced or refilled regularly.
The nitrogen plant would ensure that the correct volume and quality of nitrogen would reach the manufacturing process through a piping system.
Once the nitrogen plant had been commissioned successfully, the approval of a second C30 production line would be next. Unfortunately, it was determined that the nitrogen plant agreed upon previously is not sufficient for both production lines. As a result, an optimisation is currently being implemented by the manufacturer Atlas Copco. By April 2019, the new, larger plant should be in operation and able to supply both production lines with nitrogen from the pipeline.
Quality
By implementing the nitrogen generator, we can ensure a consistent quality in our nitrogen network. We are no longer subject to possible fluctuations in quality due to delivery batches, allowing us to produce more safely, unaffected by potential delivery bottlenecks.
Technology
In our C30 manufacturing, we need nitrogen to ensure the required soldering quality. In order to optimise our soldering results during wave soldering, nitrogen is used as a protective gas. This protective gas displaces the oxygen, thereby reducing oxidation in the liquid solder as well as on the component surfaces to be soldered and the circuit boards. The generator has corresponding interfaces that allow quality and delivery quantities to be monitored.
Do you have a concern, but no proposed solution (yet)?
No problem! Simply speak to or telephone a BVW member, or send an e-mail to the address below.
Together, we will find a way to at least improve the matter.
Contact person: Nader F. Tabbara
+49 (0) 511 6746 - 164
nader.tabbara@nassmagnet.de

This is how
suggestions for improvement work
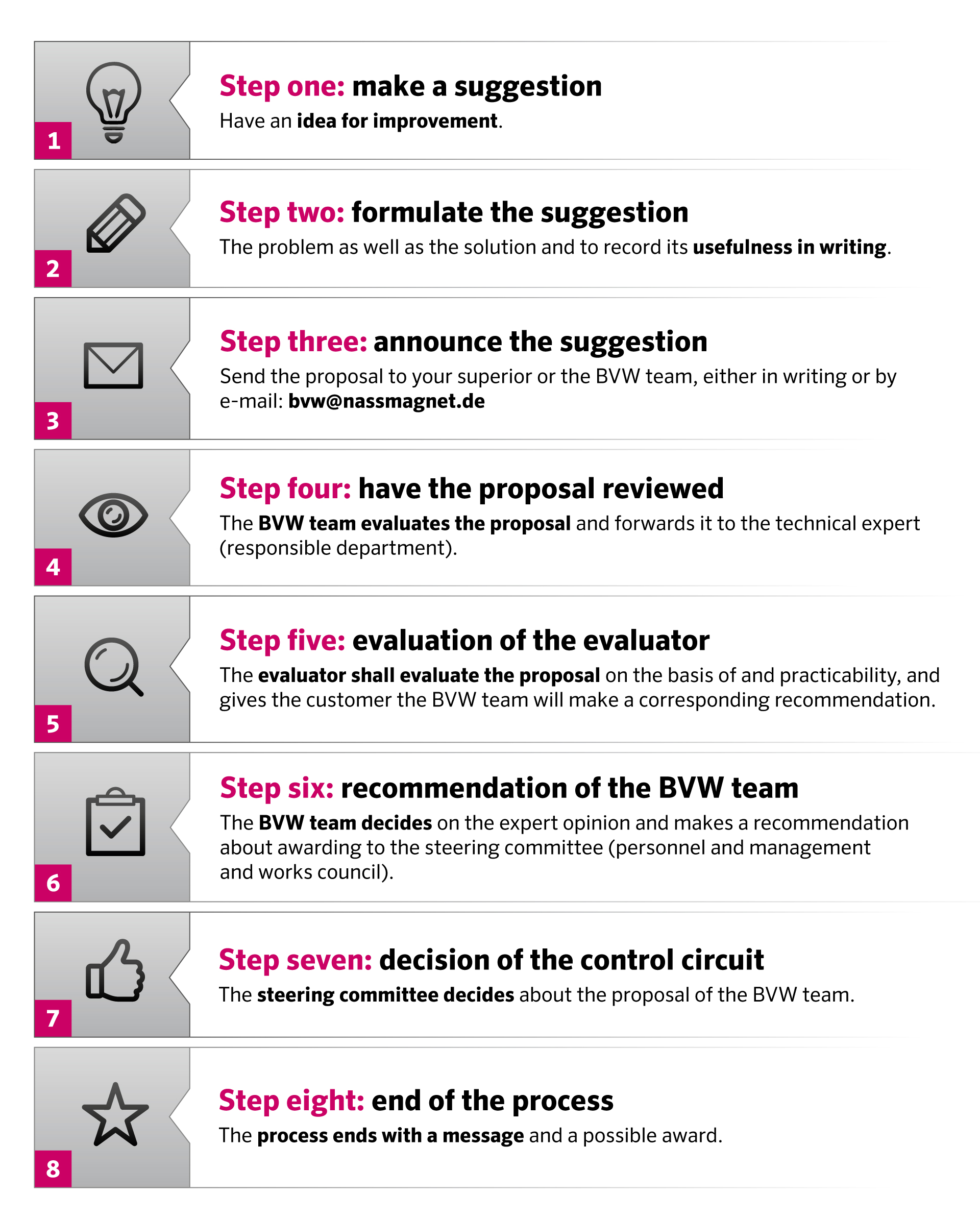