The new injection moulding machines
Precision, high repeat accuracy, economy
Innovative products and teamwork are cornerstones of our company. To hold our own against the competition, however, we need to keep pace with the technology. For this reason, we have been replacing the old injection moulding machines with more efficient models, and will continue to do so as part of an ongoing process to adapt to constantly evolving requirements. In this article, we outline how the Engel e-motion 110 optimises both production and everyday operations.
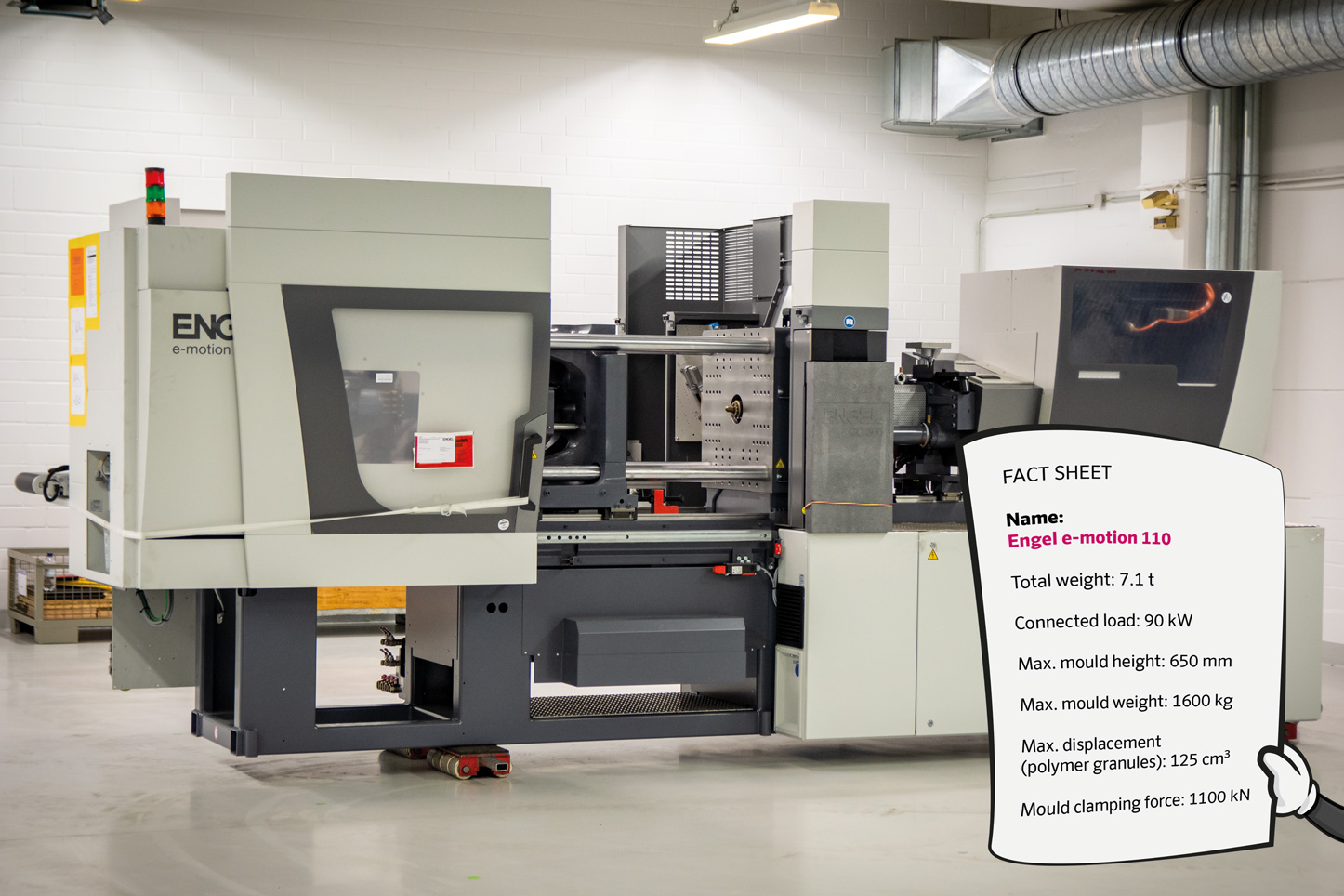
Is new always best? No. We only choose new when expedient. With defective or outdated machinery, it is impossible to survive on the market. But investments must be worth the cost, for the company and for the employees. So before making any new purchases, we must always assess whether new machines are going to pay dividends and ascertain which equipment is best suited to our needs. Aside from the financial outlay, factors such as maintenance, precision, quality and noise emissions must also be taken into consideration. Ultimately, new equipment should improve both production and the working conditions.
Engel e-motion 110
After much deliberation, we opted for machinery manufactured by Engel. The 7.1-tonne e-motion 110 won us over thanks to the myriad of benefits that it offered over and above those offered by comparable machines. Those benefits include high process reliability and repeat accuracy because fluctuating oil influences are no longer an issue. The fast set-up and take-down times coupled with reduced noise emissions make life a little easier and the work environment more pleasant.
One major factor in our choice of machine was the low maintenance costs. These electric injection moulding machines have no hydraulic components such as valves, hoses or filters that would need to be maintained or replaced. Additionally, the product series boasts a number of special features:
iQ weight control
This system „decodes“ the curve and uses this tocalculate the quantity and viscosity deviations that are relevant to the process. This enables us to achieve a consistent moulded part weight and consistent mould filling, even with material variations. As a result, the variation in moulded part weight is reduced by up to 85%.
Using this feature boosts productivity and guarantees reliably high-quality parts. The ever decreasing frequency of rejects coupled with the smooth running of the processes also makes these new machines considerably more cost-effective.
iQ clamp control
The intelligent „iQ clamp control“ solution automatically regulates the required clamping force for guaranteed component quality. This not only prevents damage to the moulds and clamping units – it also helps to eliminate rejects. And ensuring that the machines use the optimal clamping force has the added benefit of being more energy-efficient.
These systems enable machine operators to work as effectively as possible. Another advantage of the iQ variants is that, unlike with oil, the drives do not first have to establish a state of thermal equilibrium. This means that there is less waste on start-up, and the machinery can be up and running and ready for production in no time at all.
Carsten Meinhardt
Head of production, nass magnet GmbH