Quality assured!
HU reduces scrappage costs
After a change of management in 2017 and the addition of a number of new specialist staff, the Quality Assurance department in our Hungarian subsidiary nass magnet Hungária Kft. was finally in a position to fulfil the company‘s quality objectives without external input.
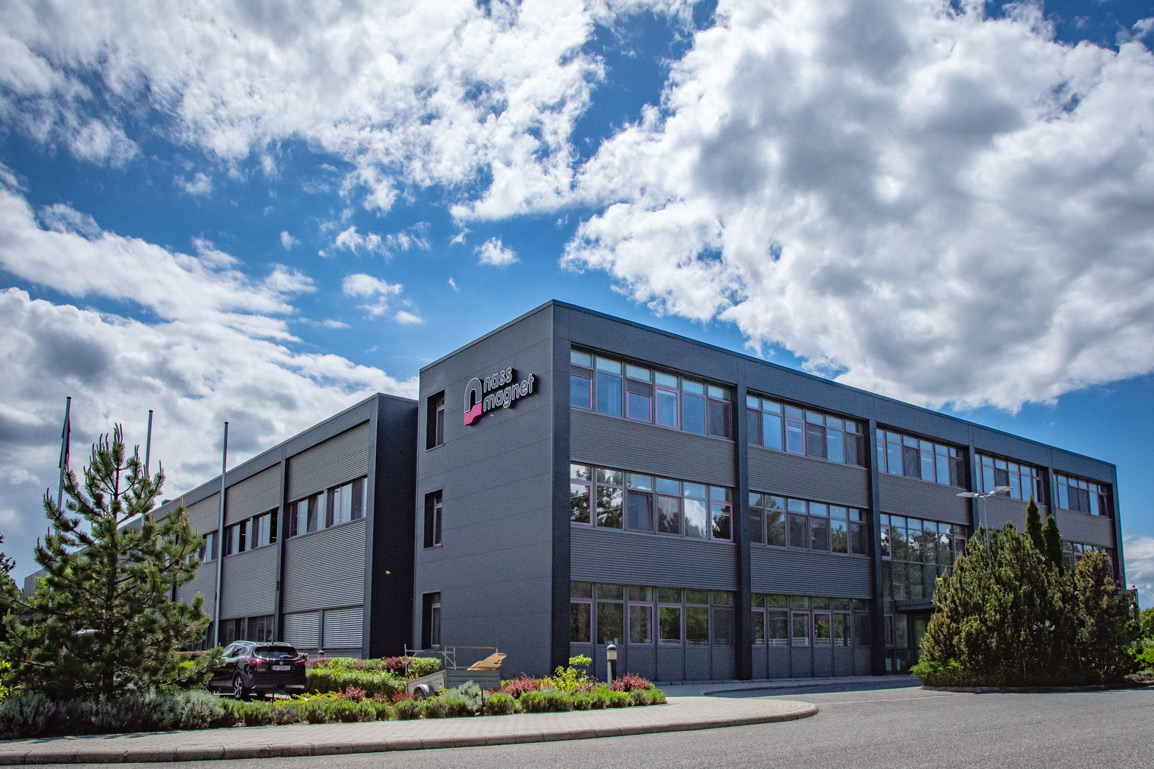
The QA department in Hungary now has all the necessary resources at its disposal to actually make headway with the job at hand. Staffing shortages in previous years unfortunately meant that the Hungarian plant‘s Quality Assurance department was just about able to tread water. Their main focus day to day was on identifying problems as they arose and rectifying them. There was simply no time for implementing preventative measures.
Long-term cost reductions can only be achieved through short-term cost increases. So in April 2018, the Hungarian Quality Assurance department took on a new QA engineer and a final inspector for each shift. The augmentation of the QA department with its new QA recruits mean that it now has the capacity to cover all production areas, as illustrated in the chart below.
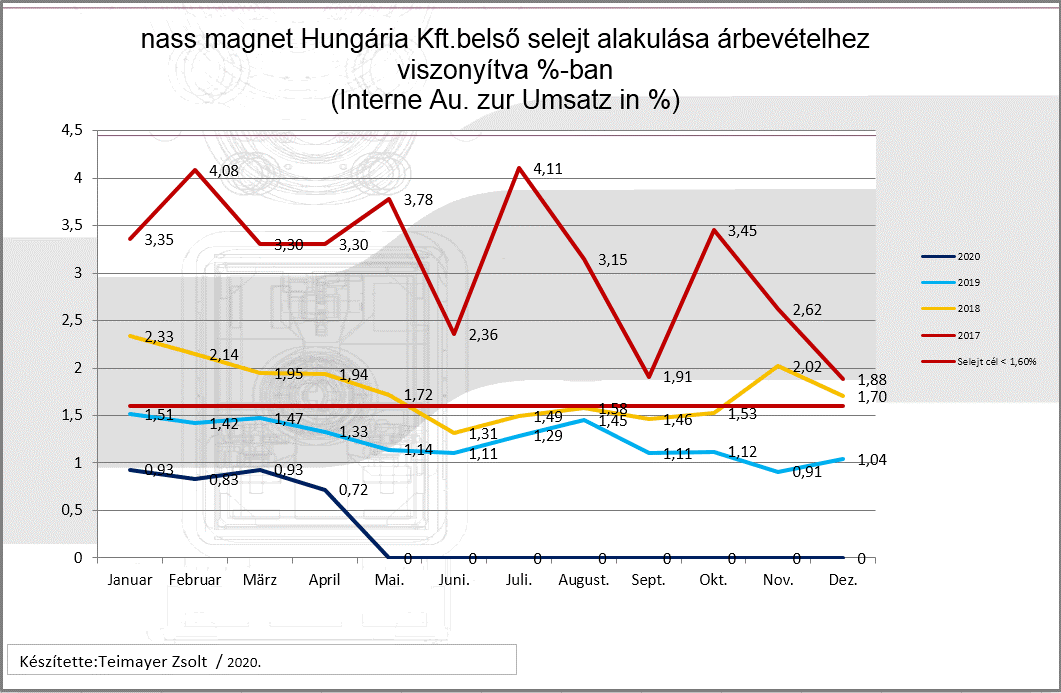
Our day-to-day activities
One of the basic prerequisites for ensuring that production runs smoothly is the ready availability of the components as required by the technical drawings. In most cases, the raw materials are subjected to an incoming goods inspection before they are put into storage and used in production.
This operation encompasses the regular incoming goods inspections themselves (which entail inspecting more than 300 products each month), and additionally involves documenting the quantity increases and providing samples of (internally produced and third-party) components. Two members of staff are required for testing mould parts and for monitoring and maintaining measuring equipment.
Our measurement laboratory is tailored to our products‘ requirements. Its facilities currently allow all sizes and qualities (with the exception of raw materials testing) to be reliably measured. During the procurement process for our measuring equipment, in order to achieve measuring system interoperability across the board we opted as far as possible for equipment that was already in use at the Hanover site.
The internal scrappage rate as a proportion of the turnover was on overage 2.61% in 2017, amounting to €565,000. So the quality objective of 2.00% set out in the BSC* for 2018 has been a significant challenge for us, but one that we have risen to admirably.
Actions and measures for reducing scrappage
The task and the objectives were clear, and so we set about identifying a solution. The first step in this process was to designate an product-specific scrappage code for every workstation in Production. The theory did not initially seem too complicated, but in practice, a usable scrappage code needed to be generated that applied to all employees equally. This code allows defects or failures to be precisely identified, as well as all expected outcomes. To make it more manageable, the scrappage code must not include too many attributes. This task proved to be far from simple, particularly when you consider that every single workstation needed to be taken into account and incorporated.
Once a consensus had been reached and the codes had been accepted by all parties, the staff had to be trained in how to interpret the individual codes. The newly designated codes for each of the workstations then had to be entered into the SAP system to allow the amount of scrap produced during each shift to be recorded. We had to ensure that the new way of working with scrappage codes was clear and comprehensible to the entire workforce and that the staff would all implement it. The coding system allows parts to be properly identified – for 2 months, every single part that was scrapped had to be inspected, assigned to groups, remeasured and characterised by the QA department.
How we did it
We realised that the most efficient approach to making savings was to start our restructuring efforts with the injection moulding process, since this constitutes the final step in our production process and it is at this stage that the most time-consuming operations take place because the greatest number of parts are installed here.
An ABC analysis** of the defects/failures was conducted for the logged scrap and found that most defects and failures occur when the machine is started or restarted.
In injection moulding, start-up scrap is produced during the first few „injections“ – normally, the first two or three production attempts result in scrap because the mould cavities are not yet completely full, the cycle time is still not quite right and the process is not yet stable.
To further reduce scrappage during machine set-up, additional measures needed to be taken. This is why we decided that scrap from those of our automotive products that generate welding waste (the product welding should be validated) should be prepared for further use rather than disposed of. The product can then be used as an adapter for the injection moulding process. In a certain sense, this could be considered recycling since the scrap is reused.
The conditioning process and further handling and processing of these scrap parts require particular care. For this reason, we had to develop a separate process that included a number of different inspection stages. We also had to teach the staff how the new system works. As a result of these measures, depending on the number of products manufactured, we are now able to save several hundred euros in the automotive sector alone.
**An ABC analysis is a business management analysis method for dividing inventory items into one of categories A, B and C

The new quality bonus
It is clear to us that our employees are key to the success of our manufacturing processes. If we want to reduce scrappage, employees should be actively involved in the process of maintaining high quality standards and should be incentivised to do so. So we have made some changes to the quarterly bonus:
To further cultivate quality consciousness amongst employees, the entire bonus is now calculated based on a 50/50 split between production performance indicators and quality performance indicators.
As part of the incentive system, the quality bonus is based on the scrappage costs in relation to turnover. The lower the rate, the higher the bonus. Four different quality factors are used to calculate the exact bonus: Waste, customer complaints, time spent on reworking, and scrappage costs.
The monitoring checklist
One of the fundamental principles of physics is the idea that movements always take the path of least resistance. The same can also be said of people. We make sure that our employees will always use the prescribed components, perform all the necessary checks and comply with the work requirements at all times during the production process.
As Stalin once said, trust is founded on regular checks, so we have introduced a „Monitoring checklist“ for our quality control inspectors to use during their daily workstation audits. Our results to date confirm that our employees have been doing their jobs properly; the key performance indicator corroborates this, with a 99% success rate in the third quarter of 2019.
First signs of success
Let‘s take a look at our product System 8 Solenoid Coil as an example: The scrappage rate for this was 4-7% due to wire breakage. By redefining the wire wrapping height, we were able to reduce the failure rate, and as a result reduced the scrappage rate to 1.3%.
It goes without saying that there are still products with significant potential for reducing scrappage. One of my favourite products is the C-13; we have never been able to get the scrappage rate for this product below 10% since it was launched. But thanks to the new, modified raw material, we can finally see the light at the end of the tunnel. Once we have introduced the new basic material, we anticipate a scrappage rate of just 5-7%.
We are currently working towards reducing and partially or even completely eliminating problems, resistance defects and failures in all our products within the next few years. When we achieve this, we will be able to save thousands more products from the scrapheap every year.
A good interim result
As a result of these measures, in just under 2 years we have succeeded in reducing our total annual scrappage costs from €565,000 to approximately €320,000 (from 2.61% to 1.3%). The evaluation below shows how our costs have changed over the following 2 years. For 2019, a value based on the average for the previous 9 months has been used.
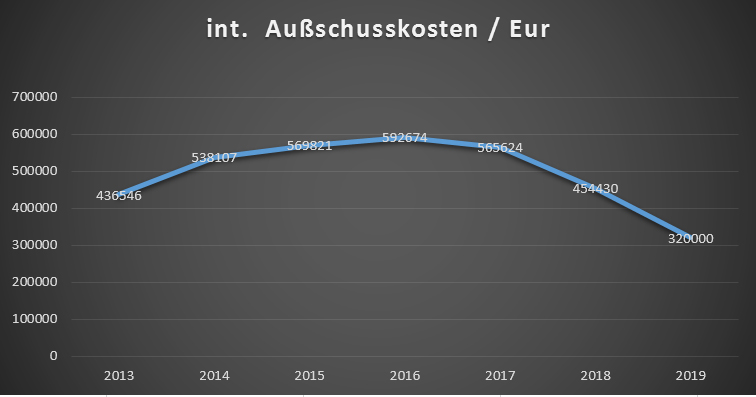
Consistent quality, fewer complaints, better results
In summary, stable, quality-oriented production processes that result in limited customer complaints, minimal scrappage and minimal reworking can only be achieved by
- engineering robust products and taking into account the manufacturing tools and technology when defining the tolerances. The more leeway there is in production, the more work will be required in order to manufacture good products.
- continually cultivating and updating employees‘ knowledge and quality consciousness. For this purpose, our staff undergo regular training.
- investing time, money and energy into ensuring that all systems are in good working order and performing preventative maintenance in order to pre-empt unwanted malfunctioning.
- designing quality into the product right from the very beginning, because quality cannot be integrated into a product retrospectively. If the quality is simply not there, products cannot be manufactured without high levels of internal scrappage, reworking and customer complaints.
We are aware that our scope for reducing scrappage is not infinite and that, sooner or later, we are going to reach the limits of our capacity to do this. It is about finding the optimal balance of scrappage costs and costs incurred in eliminating scrappage. Until then, there are still various shortcomings to remedy and products with further potential to tap.
As the years go by, the amount of scrappage reduction grows ever smaller. Over time, we want to apply the KAIZEN** philosophy by embracing the principle of continual improvement. We must train ourselves to spot opportunities for even the slightest of improvements.
**KAIZEN = Japanese life and business philosophy; a strategy that focuses on striving for continual improvement
We want to deliver results that improve year after year so that our products triumph time after time. This objective encapsulates our approach to progress at nass magnet.
Zsolt Teimayer
Head of Quality Assurance,
nass magnet Hungária Kft.